Organization of
production processes
01
Product lifecycle
management
02
Supply chain
coordination
03
Reduction of
operational costs
04
Implementation of an ERP system contributes to sustainable business growth through effective resource management
Key ERP functions for the consumer goods industry
Multi-level bill
of materials
of materials
Production
scheduling
scheduling
Order processing
automation
automation
Product cost
calculation
calculation
Raw material
supply coordination
supply coordination
Multi-warehouse
management
management
Benefits of a custom ERP system for the consumer goods industry
Reduction of operational costs, minimization of errors, and resource optimization
Automation of order processing, financial accounting, and invoicing
Multi-level bill of materials for managing complex manufacturing processes
Optimization of warehouse processes: storage, receiving, and shipping of goods
Real-time synchronization of supply chains with all partners
Control of maintenance and scheduling of repair work
Functional ERP modules for the production of consumer goods
Depending on your business needs and budget, you can choose the necessary functional modules of the ERP system to automate business processes:
Manufacturing management
Create detailed plans and coordinate all stages of production, from material testing and cost calculation to bringing the finished products to market
Procurement management
Develop procurement plans based on production needs, interact with suppliers, and manage expenses for raw materials, components, and equipment
Order processing
Automate the entire order processing cycle: from creating and planning production resources to invoicing and monitoring order status
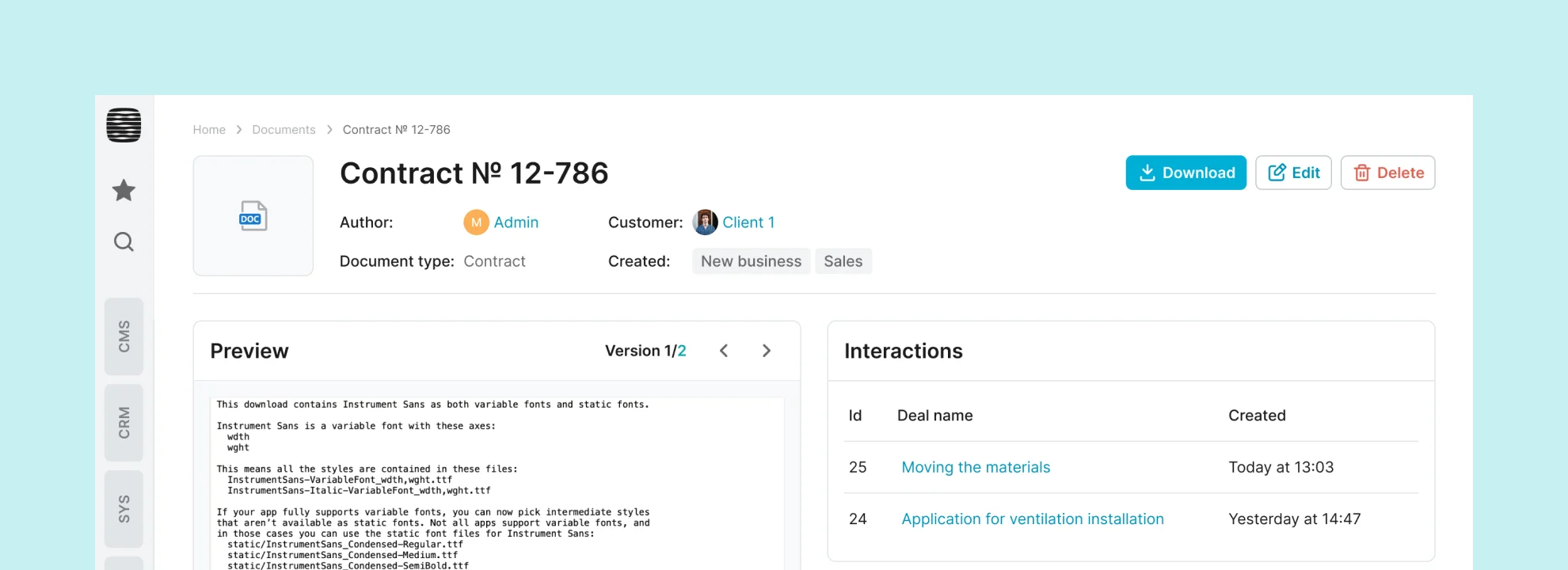
Financial management
Optimize budget management, track expenses for raw materials, packaging, and equipment maintenance, and generate financial reports across various parameters
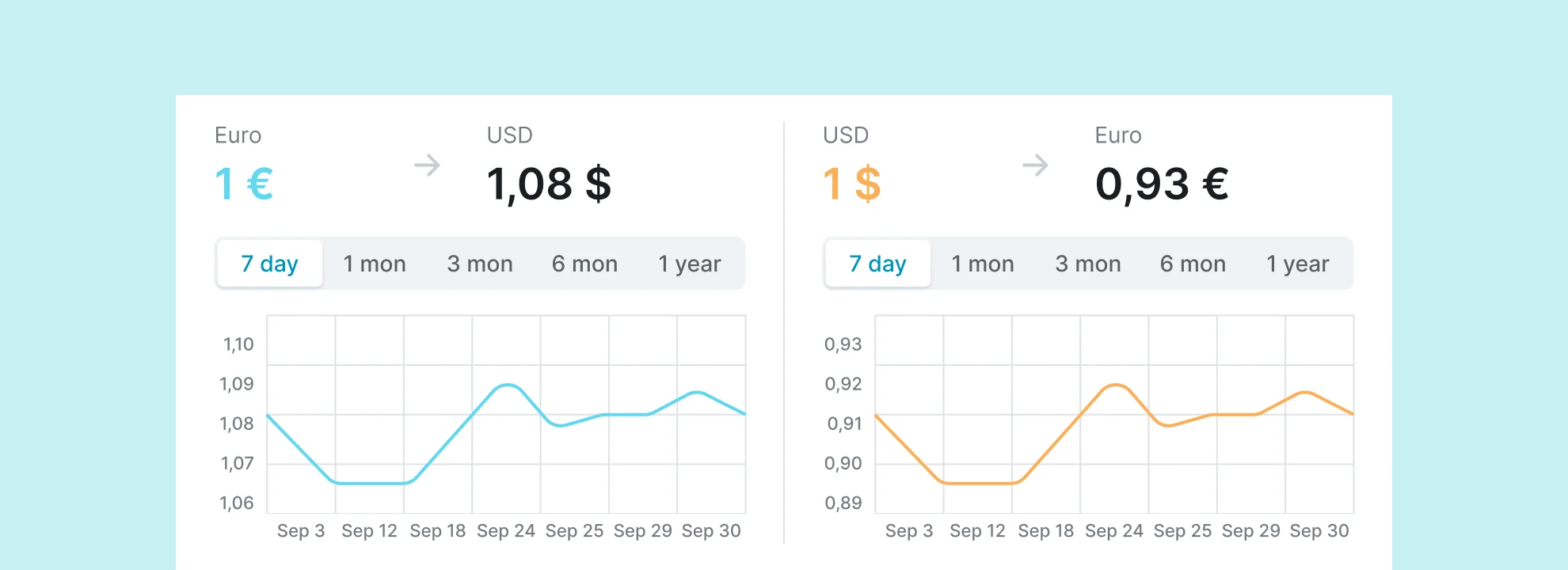
Maintenance management
Plan maintenance and repairs for equipment and machinery, effectively collaborate with service providers, and monitor the condition of production assets
Inventory management
Automate inventory management of materials and components, track the movement of product batches in the warehouse, and adjust stock levels based on demand
Supply chain management
Manage logistics processes and suppliers: from ordering raw materials to warehouse management, cost monitoring, and integration with other business processes
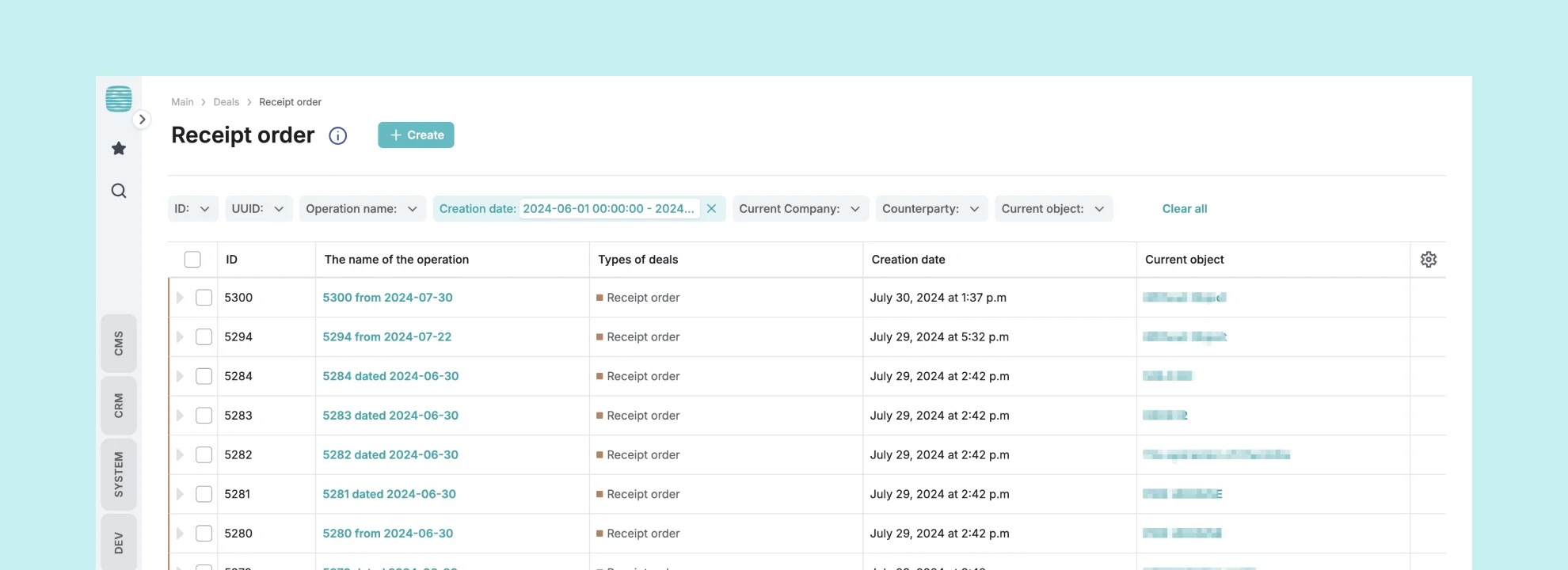
Human resources management
Create work schedules, manage payroll, manage employee training and certification, and ensure compliance with safety standards and regulatory requirements
Manufacturing management
Create detailed plans and coordinate all stages of production, from material testing and cost calculation to bringing the finished products to market
Procurement management
Order processing
Financial management
Maintenance management
Inventory management
Supply chain management
Human resources management
Custom software development for manufacturing with FreshTech
Optimize production, supply chain, warehouse, and documentation management. Fast deployment based on the low-code platform Spiro: only the necessary functional modules for the efficient operation of your company
Energy industry Electronics and electrical engineering Light industry Metalworking industry Production of wood and paper Production of consumer goods Chemical industry Production of building materials Cosmetics and perfumery Engineering Production of furniture and fittings Pharmaceuticals and medicine Automobile industry Food industry
Frequently Asked Questions
What are the benefits of implementing a custom ERP system for manufacturing?
Is it possible to integrate ERP with other systems and applications?
What manufacturing management functions does an ERP system include?
What is a Multi-Level BOM?
What are the benefits of deploying on Spiro low-code platform?
How do you implement an ERP system with Spiro?
What is the cost of ERP development for the production of consumer goods?
We'll create
an ERP system for your business
Our manager will contact you.