Custom CMMS: Integration with Third-Party Systems
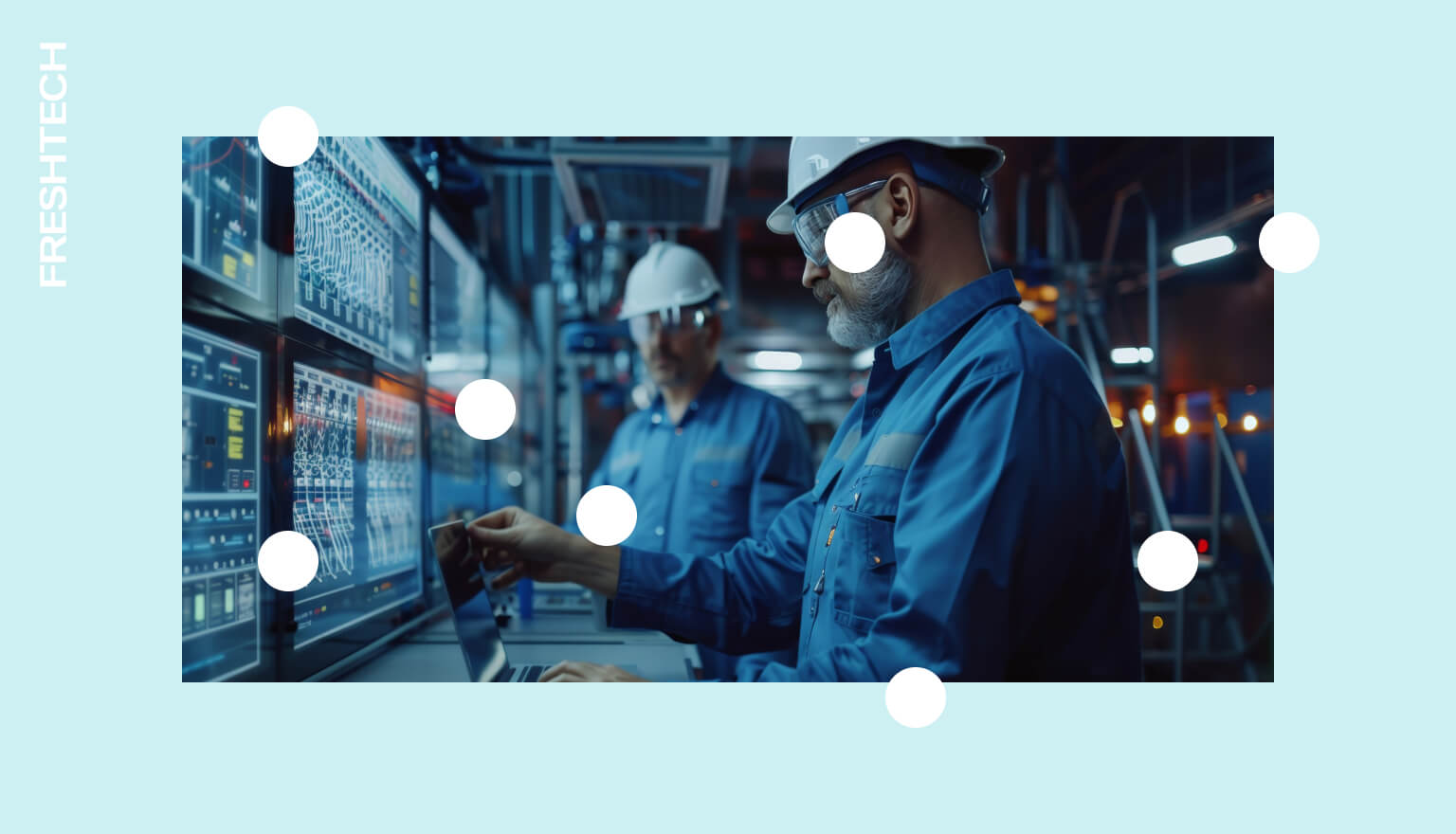
A custom CMMS simplifies maintenance management and can be easily adapted to the specific needs and business processes of a company. Integration with third-party systems creates a single centralized platform and provides a number of benefits, which we will discuss in this article.
CMMS is a maintenance and repair management system for equipment and machinery. With this solution, you can optimize workflows, simplify work planning, and provide your employees with convenient access to data.
By integrating CMMS with third-party systems, you can consolidate all information into a single platform. Reducing costs, convenient interaction between departments, and minimizing errors are just some of the benefits of this approach. Next, we will take a closer look at the main aspects of CMMS integration with ERP, CRM, and SCADA.
CMMS integration with ERP
The integration makes it possible to automatically create maintenance orders based on plans and schedules in the ERP. Work statuses get updated in real time, which ensures transparency of processes and timely completion of tasks.
Inventory management also becomes more efficient as data is synchronized between CMMS and ERP. Automatic monitoring of spare parts movement and generation of purchase orders reduce the risk of downtime due to lack of necessary materials. ERP analytical capabilities allow you to receive detailed reports, analyze productivity, and control finances and accounting.
A single platform simplifies interaction between maintenance, procurement, finance, and production departments, reducing errors and misunderstandings due to duplication and manual data entry.
CMMS integration with CRM
By centralizing data about customers and their equipment in a single system, you can access service history and previous requests. This enables technical specialists to respond quickly to requests and provide better services.
Automatically generating maintenance tasks based on customer requests reduces staff workload and minimizes the risk of errors. Setting up notifications about the status of work or the maintenance schedule helps to keep in touch with customers and increase their loyalty.
Analytics and reporting are another important advantage of CRM integration. This way, you can conduct in-depth analysis of customer interaction, identify key trends and behavior patterns. Thus, you can adapt your marketing strategies and increase conversions through a better understanding of customer needs.
CMMS integration with SCADA
SCADA is a supervisory control and data acquisition system used to monitor and control industrial processes in real time. The main function of SCADA is to collect, monitor and analyze data from various industrial facilities such as factories, power plants, water intakes, transportation systems, etc.
SCADA deals with the collection of data from sensors and devices that monitor various parameters of production processes, for instance, temperature and pressure. This data can be integrated into the CMMS to automatically monitor the condition of the equipment.
Integrated data from SCADA allows you to generate detailed reports on equipment condition, process efficiency, and maintenance costs. This helps businesses improve operations and plan future investments in technical equipment.
In this way, CMMS optimizes equipment maintenance management and planning of technical work. The system provides convenient access to data for company employees and significantly reduces operating costs.
Depending on your business needs and budget, you can choose the necessary functional CMMS modules and integrate third-party systems and services. Leave your contacts in the form and our manager will contact you and tell you about CMMS deployment on the basis of our Spiro automation system.